Fortifying Your Company Against Disruption
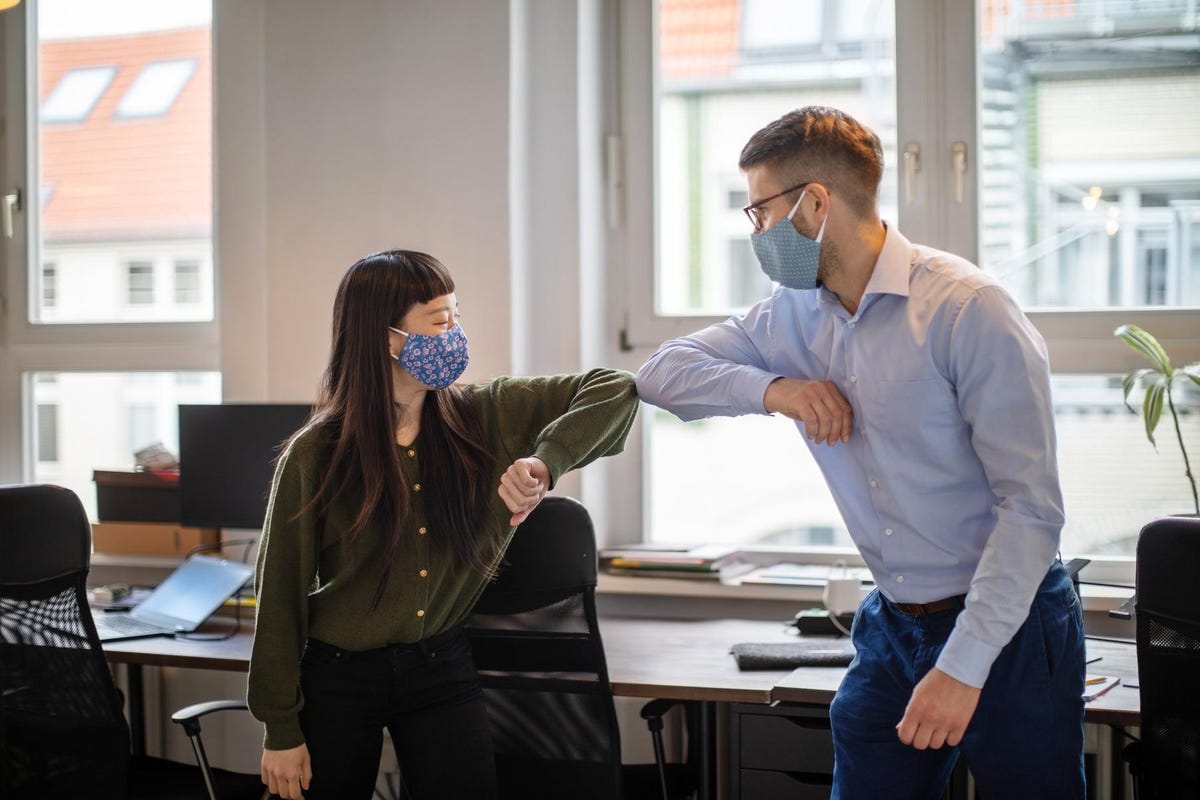
Dozuki cofounder. We are a premier Frontline Digital Transformation (FDX) tool that companies use to standardize manufacturing operations.
getty
What pandemic buzzword do you never want to hear again? New normal? Business as usual? Disruption? Social distancing? Pandemic brain? Essential business? Flattening the curve? Contactless delivery? There’s been no shortage of overused language in the last two years.
Most companies are tired of hearing about how to “navigate a crisis in these unprecedented times so you can reimagine your operations and move forward in our post-pandemic world.” But all memes aside, here’s one idea that shouldn’t be taken lightly: operational resilience.
Operational resilience is the ability of your organization to immediately respond and adapt to the changes in the environment, systems and processes in a people-centric way. It’s not a buzzword—it’s a survival tool.
Here are two important operational resilience recommendations so your organization can increase its adaptability and responsiveness in the face of new challenges.
1. Hardwire resilience into your operating system.
Identifying and responding to business moments with the right stream of information at the right time to the right person is priceless. When companies standardize their knowledge management efforts globally, companies can be more operationally resilient without dramatically increasing costs. Employees are hardwiring resilience into their operating system and, in turn, figuratively hardwiring that pattern of behavior so it becomes instinctive.
The global pandemic has taught us that businesses can no longer rely on phone calls, emails and Slack messages to their experts to solve all their problems. Employees with valuable skills are busier and scarcer than ever, so they need the ability to pass on their knowledge once, document it forever and deploy it globally to elevate the collective intelligence of the team.
Here are some tips you can use within your own company.
• If you don’t write it down, it never happened. Operational resilience is often a simple matter of documentation, particularly when retention is low, turnover is high and the job market is fluctuating. The lack of a knowledge transfer mechanism prevents new hires from being productive and causes production problems. One rule we tell our customers is, “If you have to ask a question more than once, create a guide for it.” Don’t rely on human memory, the most fickle organism in all of nature.
• Enable offline functioning for low-signal areas. If your company has facilities that span multiple lots, Wi-Fi won’t be available every square foot. Thick walls may impede the signal, and dead zones are likely to creep up. If so, ensure workers have the ability to view their procedures, work instructions, company wikis and other key documents in offline mode. If employees need to download the information they need before going to an offsite location or some other low-connection area, they’ll be equipped to personally and quickly respond to any challenge that arises.
• Make security and privacy the foundation. Technological transformation at your company isn’t necessarily about scaling up—it’s about meeting your unique workforce needs. Perhaps you run nuclear facilities, fulfill government contracts or amass millions of pieces of consumer data. You’ll require a higher degree of security and safety than other industries. And that’s a good thing. It’s a value-added selling point. Whatever digital transformation solution you use, make sure private cloud options are available. Ensure sales and market teams reinforce that employee computers, phones, tablets and other tools have world-class security.
2. Sell digital transformation from the bottom up.
If you’re starting with technology, you’re starting wrong. Operational resilience in manufacturing starts with people, and the technology comes later. When you empower and equip employees to anticipate and respond to events, it creates a rising tide that lifts the whole organization. The ability of your organization to immediately respond and adapt to the changes in the environment, systems and processes is what will help protect your business against events beyond your control.
The challenge is that too many companies aren’t as inclusive as they could be. Traditional approaches to workforce training, knowledge management and quality management are limited to only certain stakeholders within the company.
Don’t let technology trump the real asset. In our experience working with hundreds of manufacturing organizations, machines aren’t actually innovating anything. People are the source of all your competitiveness.
Here are a few action items for your organization.
• Accept that you work in the people business. No matter what your company makes, it’s the people that help them make it. Your job is to take the people and connect them with technology, skills and processes to do the work. The myth of automation is that you’ll automate yourself out of human employees. But you still need people to buy the robots as well as service and install them. People aren’t going away. They’re an invaluable part of the process.
• Achieve small victories first. If you plan to pilot a digital initiative at your company for process management and training, this doesn’t require a huge, full-blown investment and can be a means of testing the waters of various digital solutions. If you have more than one facility, office, factory, location or building, focus on executing a successful use case that can be replicated and ported over to another team.
• Diversify centers of influence. We suggest bringing in stakeholders outside of your focus area to get more buy-in for future advancements. Doing so makes you more resilient, as influencing the broader group about change doesn’t fall on one person’s shoulders. Create a diversity of change agents who can step up to sell transformation from the bottom up, and you’ll reach more decision-makers faster.
With these tips, your organization can increase its operational resilience. When the next market downturn, pandemic or other global event disrupts the status quo, your team will be better equipped to respond and adapt to the changes in the environment, systems and processes in a people-centric way.
Forbes Technology Council is an invitation-only community for world-class CIOs, CTOs and technology executives. Do I qualify?